The Corn Exchange, Doncaster: Advice about replastering and salt contamination.
Introduction
Doncaster Council and Group Ginger, their architects, are currently working on refurbishing the Corn Exchange in Doncaster. They approached M Womersleys for some advice about the internal plasterwork repair on this Grade II* listed building, which underwent some insensitive ‘repair’ works in the 90s. They specifically requested advice for areas where the gypsum plaster has been partially stripped off and now remediation repair is required. There is concern about the interaction between the old and new plaster and the robustness of any repairs.
M Womersleys set the results of an inspection of the fabric in the areas of concern on the 17th of January 2024, a methodology and specification for treatment and the plaster repair works, using materials as appropriate as possible for this historic building with a modern floor.
The Historic Context
The Doncaster Corn Exchange is a notable historic building in Doncaster, South Yorkshire. It was officially established in 1852 primarily to facilitate trading corn, grain, and other agricultural products. It aimed to provide a central marketplace for farmers, merchants, and traders to conduct business.
The building was designed by architect Edward H. M. G. Wilks, who submitted plans combining functionality and aesthetic appeal. The Corn Exchange featured a grand neoclassical design, characterised by its elegant façade and spacious trading hall. The structure is formed from decorative curving ironwork to form a large uninterrupted space and brick with stone accents, showcasing large windows and a prominent entrance. The interior was spacious and designed to accommodate the bustling trade of grain and cereals. Notably, the building includes decorative plasterwork and elaborate detailing, typical of the Victorian era, emphasising its importance as a public building.
From its opening, the Corn Exchange served as an essential commercial center in Doncaster, facilitating local agriculture and supporting market trade in the region. The building hosted the corn trade and served various functions over the years, including housing market stalls and local traders. As agricultural practices evolved and the demand for such centralized exchanges diminished, the Corn Exchange experienced a decline in use. By the late 20th century, it became less of a commercial hub. In the 1990s, the building underwent various repair and restoration efforts as part of a broader initiative to preserve the architectural heritage of Doncaster. Despite insensitive 'repair' works that impacted its fabric during this period, ongoing conservation efforts aimed to restore its historical integrity. The building is classified as a Grade II* listed structure, highlighting its architectural and historic importance. The Doncaster Corn Exchange is more than just a trading venue; it represents the city's social and economic heritage. Its continuous redevelopment and preservation efforts underline the community’s commitment to maintaining its historical identity while adapting to contemporary needs.
The Results of the investigations by M Womersleys
A ‘Moisture Content & Fabric Survey’ had already been carried out within the building, and M Womersleys' report was built on this previous survey to explain the causes of the dampness more fully. In some areas, intrusive tests were carried out as part of the earlier fabric survey, in the areas. These locations generally showed lower moisture content on this northeast elevation, with lower ground levels. However, in one location, high moisture levels of up to 43% were found at a height from the floor of 100 mm. Over the whole area, salts were identified as being present up to heights of 160 mm, but they were not quantified.
For each area of exposed brickwork at the lower level on the north-eastern internal elevation, see photo 1, semi-quantitative tests were carried out to determine the concentrations of salts in areas of concern. The brickwork was contaminated with 400 and 800 mg of Sulphate Salts per litre of water at 600 and 800 mm above the existing floor.
Diagram 1: Semi-quantitative test results for Sulphate Salts from location A to H and for Nitrite and Chloride Salts from location A.
Photos 1 and 2: The exposed brickwork areas require treatment and replastering, and the floor is built up with layers of reinforced concrete and a dense concrete screed over compacted sandstone and a membrane.
Sulphate salts within the walls will have come out of the brickwork and the mortar after being carried by earlier water movement. Still, some could result from the wall being covered with Limelite renovating plaster or similar applied in the 1990s. This plaster likely comprises ordinary and specialist cement, expanded perlite aggregate, limestone flour and hydrated lime, dried and graded fillers, fine aggregates and chemical modifiers. The finish coat, perhaps Limelite High Impact Finishing Plaster, comprises a blend of retarded hemihydrate gypsum plaster, hydrated lime and limestone flour with organic additives. When saturated, the undercoat and top coat plaster will release salts into the building fabric they decorate, and part of the sulphate residues could, therefore, originate from these latter applied plasters.
The sulphate salts in the surface of the brick and mortar could be reduced to acceptable levels that won’t subsequently transmit through new plaster applied to the brickwork by applying a clay poultice after cleaning off all the old modern plaster residue with a nail gun or similar.
Background Notes on Salt Contamination
Salt contamination in historic buildings, often referred to as "salt-damage" or "salting," is a common issue that can significantly impact the integrity and appearance of such structures. Salts usually originate from groundwater or infiltrating rainwater that carries dissolved salts from the surrounding soil or building materials. However, many historic buildings were constructed using materials containing natural salts, such as certain types of stone or mortar, and inappropriate repair plasters at the Corn Exchange. These salts can become soluble when wet and migrate through the masonry. Insensitive repairs using modern materials, such as solid concrete floors with little drainage below and cement, can trap moisture and salts, preventing proper evaporation and leading to salt buildup.
Moisture can be drawn up old walls, through porous materials (like brick or stone) by capillary action, bringing salts with it as it rises. Salts can crystallise within the porous materials of the building as they dry, causing expansion that leads to cracking, spalling, or disintegration of bricks and mortar. Salt deposits often appear as white efflorescence on surfaces and can break down plaster and paint, leading to peeling, flaking, and other surface damage. The moisture associated with salt contamination can promote mould growth and other biological issues, further degrading the building materials.
Our findings and suggestions for replastering
Improvement of drainage and steps to reduce water movement in the building will help eliminate the problem. M Womersleys suggested that after such works, clay poultices be used to draw out soluble salts from affected materials. This method involves applying material that absorbs the moisture and salts, allowing for cleaning of the substrate.
This poultice should be applied approximately 15 – 20 mm deep to a relatively dry wall and allowed to dry out. Once dry, it will have pulled salts out of the wall and needs to be removed and disposed of. The wall should then be dry brushed down, and another coat should be applied and removed in the same way.
If no more water movement and salts rise through the brickwork, the walls could be replastered in most lime plasters. However because of the presence of water in the lowest levels of the walls, based upon the previous survey, it is suggested that a more robust lime plaster is used. This water build-up is most likely the result of the modern floor abutting the brick walls, which is likely holding water in the crushed sandstone sub-base below the concrete, with the concrete above not allowing any through, meaning it is pushed into the adjacent brick walls, that have no damp proof membrane, unlike under the modern floor.
Therefore, it was suggested that at the lower skirting level, this is rerun in-situ using 1 part Natural Prompt Cement (not an OPC-based cement but a very strong hydraulic lime, used in this country from the 1830’ s to the 1900s), to 1 part sharp sand for the undercoats and citric retarder, to allow it to be formed before it sets, and continuously built up, finishing with finer sands in the last coat. The brickwork must be primed with the same 1:1 mix but in a wetter state. All layers should be applied on the same day, green on green. The decorative dado rail, the edges to the recessed roundels and the decorative edges to the sunken rectangular panels could be formed with the same material.
However, such a mix will not only have no water permeability but also no vapour permeability. Whilst this is necessary for skirtings, which will get wet and salt damaged behind, they are really unsuitable for the plaster above this level if the water levels in the wall remain low, as per the last measurements during the fabric survey. It was therefore suggested for the plaster that a weaker and more vapour permeable mix of one part prompt to two parts sharp sand be used for the undercoats and finer sand for the top coats, as listed below, with some of the prompt replaced with Otterbein NHL3.5 to give more open time for the run work and finishing if required.
However, despite these proposed plasters being very resistant to impact damage, excessive water movement in the future will damage any applied solid plaster over a long period of time. When the lower part of the wall is complete and before the decorative dado rail is finished, the plaster above the dado rail should be patched with like-for-like Tarmac Renovating Limelite plaster.
Much weaker lime plaster could be used on the walls of this building if the floor were being replaced with one that had a free-draining sub-base, but keeping the existing floor and its potential to push water into the brick walls necessitates the choices set out above.
Managing salt contamination is crucial for the preservation and longevity of historic buildings. A comprehensive understanding of the underlying causes, combined with tailored remediation strategies, can help mitigate the effects of salt damage and protect these important structures for future generations. Consulting conservation professionals experienced in dealing with historic materials and techniques is often essential for effective treatment and restoration.
Related Articles
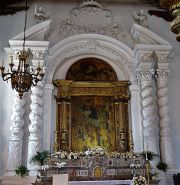
On Sunday, March 16th, why not come for a full introduction to lime plastering and a practical demonstration workshop?
Learn more about traditional clay, lime, and ornamental gypsum plasters and their use internationally…
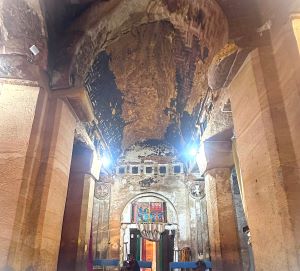
Proposals to carry out a conservation assessment at Wukro Cherkos, with a full training programme for recent graduates from Mekelle University and government bodies responsible for regional conservation work.
Introduction In response to continued concerns about the condition of one of Tigray’s most well…
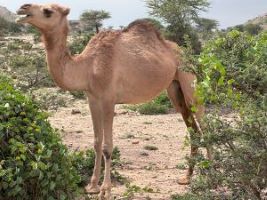
Report on the support given by M Womersleys to Jabir Mohamed at Berbera Museum, Berbera, Somaliland, over two weeks from the end of October 2024
Contents  …